Truyền động tuyến tính - Linear Motion
Take Your Production to the Next Level with Smarter Manufacturing Solutions.
We incorporate state-of-the-art designs, components and digital technology. We design, manufacture, and customise linear motion and linear actuators, including smart actuators, linear guides and ball and roller screws for a variety of industrial applications that help customers shift to electrified solutions.
Take Your Production to the Next Level with Smarter Manufacturing Solutions. The largest, aluminum extrusion, electro-mechanical, linear actuator manufacturer, in Taiwan and Mainland China. Professional and responsibility is always the cooperate concept of Toyo to create high quality product with low cost.
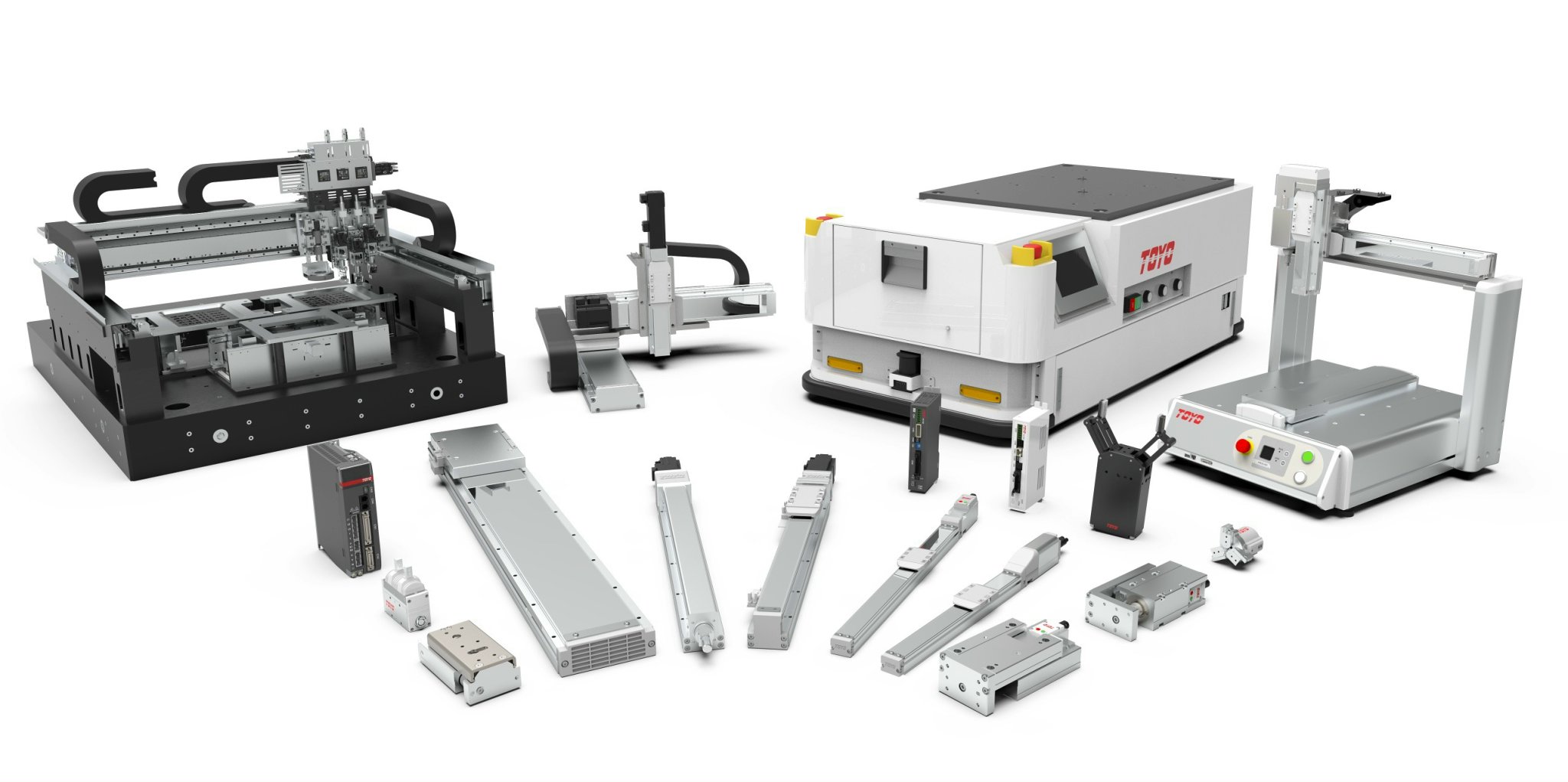